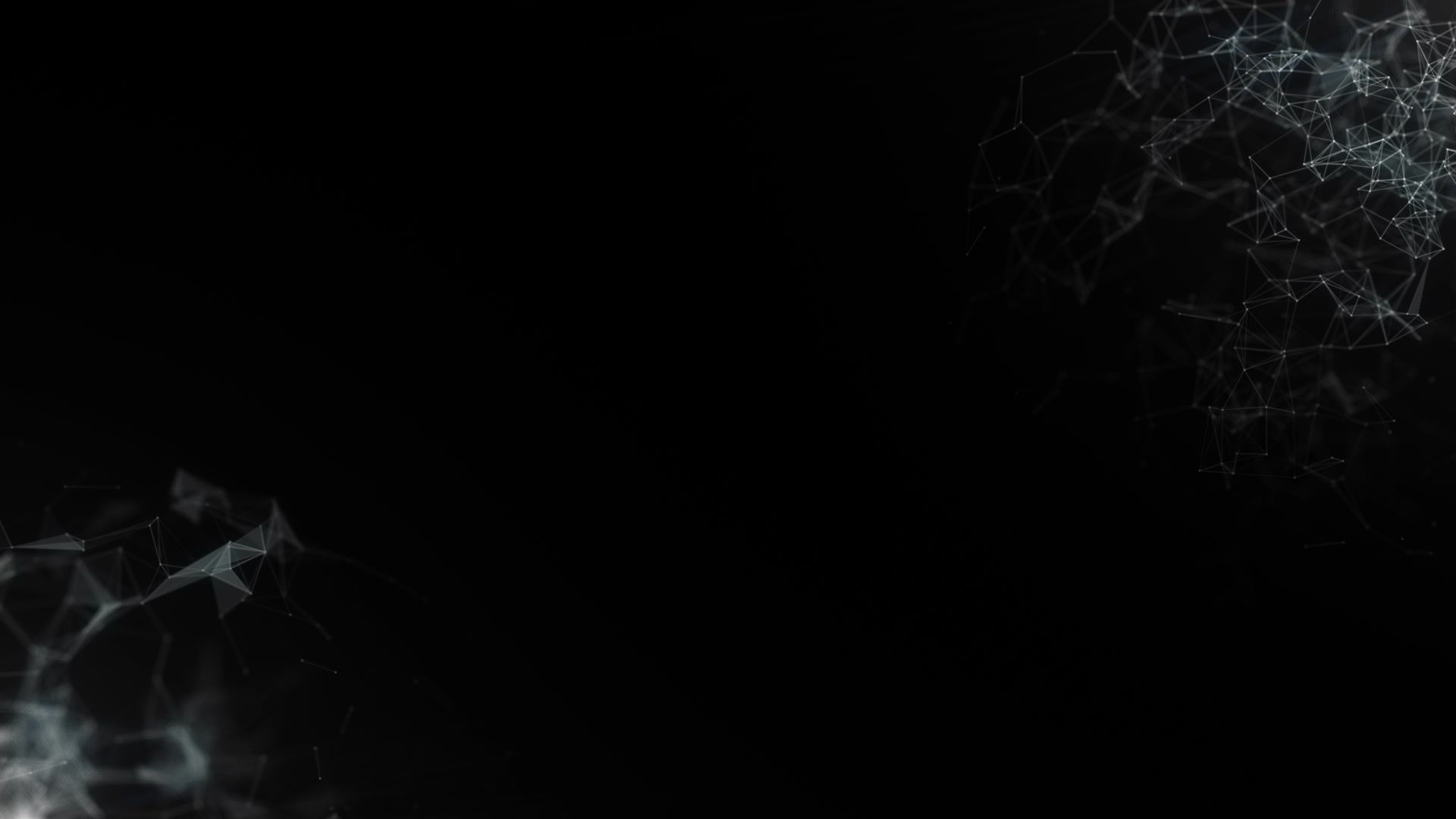
Process

Current Timline:
1-22: visit to Sacred Stone
1-25: TIG cert + manifold construction + boulder event
1-25-> 2-1 Manifold construction
2-1->2-8 clean testing in denver
2-10--> 3-1 set up and live testing in ND
​
​
more maths...
​
​
Digestate flow rate is:
330 ft^3/ 20 days= 16.6ft^3/day / (24hrs * 4 times/hour) = 1/3 ft^3 per addition, every 15 minutes
With feeding also should come bubbling, I am not sure of the optimal bubble flow rate, but accomodate
and the gas flow rate should be about 7-15 cubic meters per day, which reduces to:
7,000-15,000 liters/ (24*3600)= 15,000/ 86400= ~ .17, with potentially a max flow rate of .25 liters/s
That's the production gas rate,
The bubble mixer should pump a considerable flow rate out of the reservoir and back through the digester , say 5 liters/s.
​
Compared to this the production rate is negligible
and next is hte methane gas flow rate... this is related to the heat loss of the system,
​
estimate the heat loss at ambient air temperature of 50degrees F (10C), with a liquid temperature of 130 degrees (55C)
​
assuming the floor is perfectly insulated and all losses are made to free unforced air with a velocity of zero heat transfer coefficeint
​
h= 10.75
​
then the needed heat flow is 2250 W, the caloric value of methane is 1.1 e6 joules/ cubic foot,
​
this results in a flow rate of .0579 liters/second of methane- not counting the heat=up energy needed every 15 minutes to account for the fluid addition.
​
1/3ft^3 * (delta T = 80F)* (Cp of water= 62.34 btu/(ft^3*F))= 1662.4 BTU= 1.754e6 Joules
​
This value is roughly 1.5 cubic feet of methane, split over the 15 minutes interval results in a flow rate of .1 cubic feet per minute and
​
.0472 liters/s
thus the total methane combustion flow rate would need to be approximately:
.1 liter/s
The stoichiometric ration for methane gas to air for complete combustion is 9.5:1,
​
resulting in a max air flow rate of about 1 liter/s through both input air and combustion exhaust pipes.
​
https://www.engineersedge.com/heat_transfer/convection.htm
(air heat loss coefficient)
http://www.engineeringtoolbox.com/convective-heat-transfer-d_430.html
(heat loss convection)
http://www.ocean.washington.edu/courses/envir215/energynumbers.pdf
(calories of fuels
​https://en.wikipedia.org/wiki/Human_feces
​
Sizing and yield:
The Digester will need 20 days of hot fermentation to develop the majority of the gas available within the compost, this works out to a tenth of a pound of waste requiring about a cubic foot of digester space.
​
.1 lbs waste/ day/ cubic foot digester
IBC= 330 cubic feet
Average human waste= 1 lb /day
​
So 1 IBC container can handle the daily waste of about 30 humans (conservatively)
​
The gas yield per pound waste should be about .24-.48 cubic meters
​
And the heat yield per cubic meter of gas: 6kWhr / cubic meter
(unfortunately the conversion to electricity in a generator would probably only yield 1-2 kWhrs/cubic meter)
​
So then 1 IBC methane digester should yield between 6-12 kWhrs of heat per day, if it were running at capacity in a camp of 30 people.
That's enough gas to boil 230+ gallons of water from freezing- plenty to run a kitchen, all the generators you could like, and probably even a foundry or a kiln!
​
​
A living Process:
It is important to understand this is a living process, because being alive, it can die! Methanogens are a somewhat finicky bacteria, and they operate best at completely steady state: while being fed a constant amount of the same sort of feedstock at a constant temperature, alkalinity and acidity levels. ​
​
Current commercial methane digesters have much larger volumes (usually used for huge livestock operations), making the affect of the inputs smaller relative to the whole volume. In a small system this instability can be offset by a fine control system using sensors, heaters, coolers and metering small regular additions of waste.
​
This will be a learning process both in optimizing this sensing and control system, as well as for each individual operator at every camp. The "bugs" (methanogens) will react and live and even evolve differently in different climates and with different camps. The diet of the camp itself will be tied to the digesters performance, and the maximum gas yield will only be achieved as the technician gains experience and learns to cater to the preferences of that digester's bacteria.
​
​
​
​
​
​
​
​
​
Important points here-
-since this digester is predicted to produce .25 liters of methane and consume .1 liters for the purpose of maintaining temperature,
​
Also, as i think of it now, the feed-digestate heating could and should be partially offset with a heat exchanger which would be heated by the outflow-effluent
​
Also, I left some considerations out here- already wondering if anyone would read this level of technicality
I bbelieve these calculations assume that %100 of the combusted methane heat be recovered by the digestate. This is a design consideration, and an almost acheiveable goal- but to be safe there are more calculations/considerations that I skipped
​
Namely, heat flux as a function of exhaust flow rate and flame temperature- these are going to be rough anyway assuming complete combustion- which is a tricky important piece as well.
​
All these factors are workable- but realistically they'd have to be worked out- ensuring enough Time, Temperatuire and Turbulance for complete combustion, and then enough length/surface area of the exhaust pipe to fully disperse the heat into the digestate before exiting it.
​
​
I guess its important to note that human waste was a HUUGE problem at the NO DAPL protest- so these designs were a little rushed- even if they barely warmed themselves and nothing else (which even these rough figures indicates) it would be a huge improvement